Supply Chain Leaders focus on satisfying their customers. Managing key customer requires a lot of efforts and we need some metrics to make sure that the operations are efficient. In that regard, On-Time In-Full (OTIF) is the vital part of this process.
What is On-Time In-Full (OTIF)?
On-Time In-Full (OTIF) is a critical key performance indicator (KPI) in supply chain management. It measures the percentage of deliveries that arrive at their destination on time and in the correct quantity.
OTIF is essential for evaluating supplier performance and ensuring customer satisfaction. A high OTIF score indicates a well-functioning supply chain, while a low OTIF can signal inefficiencies and potential disruptions.
How to Calculate OTIF?
The OTIF formula is straightforward:
OTIF (%) = (Number of On-Time, In-Full Deliveries / Total Deliveries) × 100
A delivery qualifies as OTIF if:
- It arrives within the agreed-upon delivery window.
- It contains the correct quantity and quality of products as ordered.
- Both criteria should be satisfied to hit the OTIF for that specific delivery.
For example, if a company ships 1,000 orders and 850 meet the OTIF criteria, the OTIF score would be:
850 / 1000 × 100 = 85%
There might be two different OTIFs to take into account such as inbound and outbound OTIF.
Inbound OTIF – This is where we track the supplier’s OTIF against their purchase orders.
Outbound OTIF – This where we measure OTIF on your own outbound orders to your final customers. For final customers, there are also calculations based on promise to delivery date and customer requested delivery.
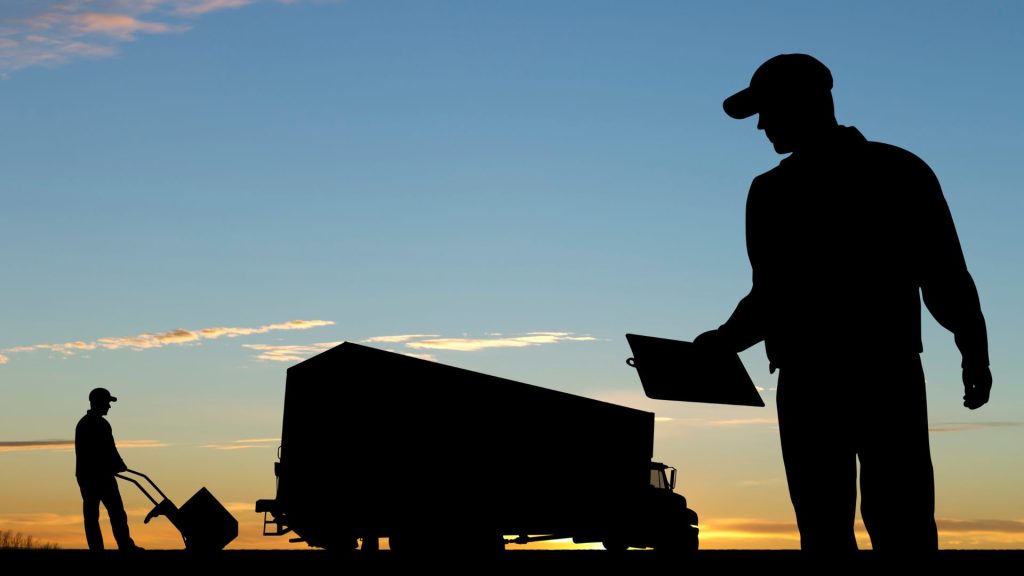
On Time in Full
Why is OTIF Important?
- Customer Satisfaction: Meeting delivery expectations builds trust and improves relationships.
- Operational Efficiency: A high OTIF reduces costs associated with delays, returns, and stockout.
- Competitive Advantage: Companies with strong OTIF performance gain an edge in the market.
- Supply Chain Resilience: Monitoring OTIF helps identify bottlenecks and improve overall logistics performance.
Factors Affecting OTIF Performance
Several factors influence OTIF, including:
- Supplier Reliability & Production Capacity – Consistent production and shipping schedules.
- Logistics and Transportation – Efficient freight management and carrier performance.
- Warehouse Operations – Accurate inventory management and order fulfillment.
- Demand Forecasting – Proper planning to meet customer demand without overstocking or shortages.
- Communication and Collaboration – Clear expectations between suppliers, distributors, and customers.
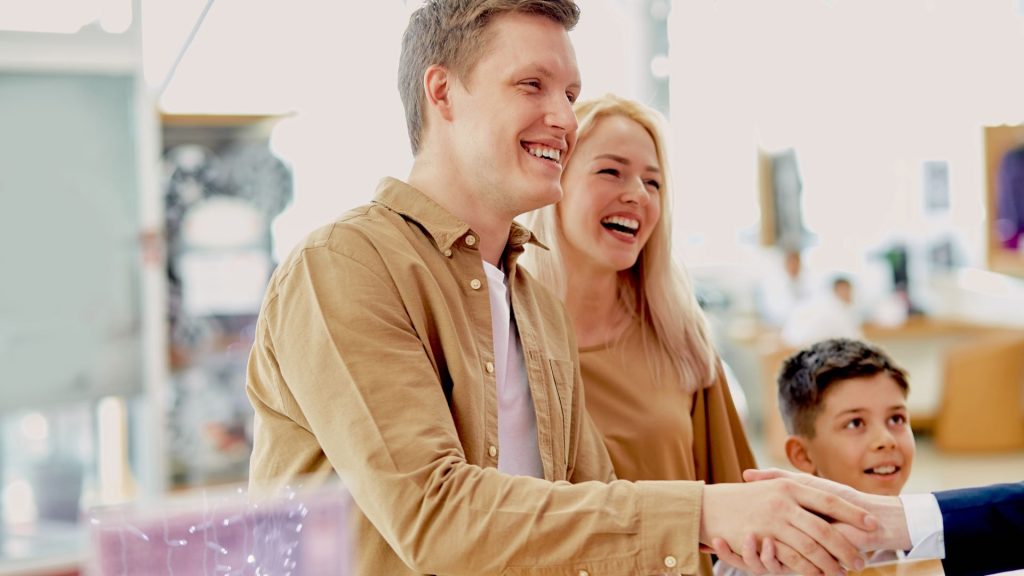
Strategies to Improve OTIF
1. Strengthen Supplier Relationships
Work closely with suppliers to ensure they meet delivery commitments and maintain product quality.
2. Optimize Inventory Management
Leverage demand planning tools to avoid stockouts and excess inventory.
3. Improve Logistics and Transportation
Partner with reliable carriers and utilize route optimization technologies.
4. Enhance Warehouse Efficiency
Implement automated systems for picking, packing, and shipping to reduce errors.
5. Utilize Data Analytics
Monitor OTIF trends and identify patterns to take proactive measures. Focus on perfect order methods to avoid any errors while capturing the customer order.
Final Remarks
On-Time In-Full (OTIF) is a key metric that directly impacts supply chain efficiency and customer satisfaction. By understanding the factors that influence OTIF and implementing best practices, businesses can enhance their supply chain operations and drive growth.
Have you faced OTIF challenges in your supply chain? Share your thoughts in the comments below!
2 thoughts on “On-Time In-Full (OTIF): The Key to Supply Chain Efficiency”